3D Sensing
Industry-leading 3D Sensing Technology
Since developing the patented narrow bandpass filter technology behind the revolutionary Microsoft Xbox Kinect gaming console, VIAVI has combined the precision of industry-leading optical filters and light shaping optics (LSO) with the scale and reliability of high-volume manufacturing. As advanced 3D sensing is introduced to cell phones, cars, and industrial robots, VIAVI continues to support its safe, accurate, and efficient use on a global scale.
What is 3D Sensing?
Three-dimensional (3D) sensing is the process of obtaining length, width, and depth information electronically and using this data to improve the interfaces between humans, devices, and the world. 3D sensing technology uses near infrared light reflection, geometric principles, photography, and advanced computing power to enable machines to “see” people and objects in a detailed, meaningful way.
- The home gaming industry provided the first practical application of 3D sensing for consumers, with time of flight (ToF) sensors capturing the gestures and movements of players to create a new interactive gaming experience.
- 3D sensing applications have expanded to include facial recognition features that enhance the security of laptop computers and mobile devices while improving digital photo quality and resolution.
- Using 3D sensing, virtual reality (VR), or augmented reality (AR) can combine real-world 3D images with computer-generated projections to create or supplement visual experiences in many applications.
- Transportation, industrial, and medical processes also benefit from the safety and efficiency gained through advanced world facing 3D sensing technology.
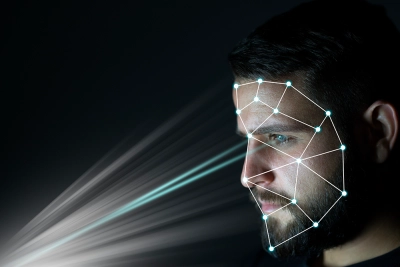
How Does 3D Sensing Work?
The technology behind 3D sensing is based on the projection of a light source toward an object and the collection of the same light waves after reflection to determine the shape and position of the object. Monitoring of a specific projected wavelength known as the “desired signal” throughout the process is a key factor.
Optical components shape and direct the outgoing light waves so that the illumination pattern of the desired signal is optimized. On the return path, focusing optics funnel all reflected light into a filter which separates the desired signal from erroneous light signals. This light is then directed to a sensor so that distance, shape, and depth information can be calculated.
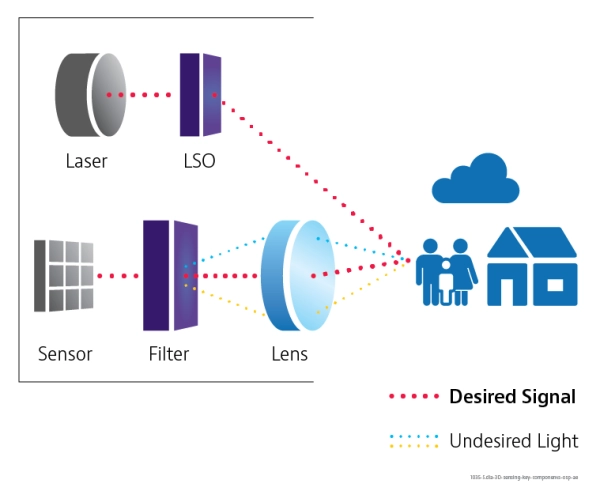
Types of 3D Sensing
Two primary categories of 3D sensing technology are known as Time of Flight (ToF) and Structured Light (SL). Each sensing method lends itself well to multiple applications, depending on the specific requirements of the user.
- Direct Time of Flight
As the name suggests, Direct Time of Flight (DToF) 3D sensing uses short, timed pulses of light followed by a direct measurement of the reflected light’s return time to determine the position of an object. Much like ultrasound or sonar, the resolution of this method depends on the volume and speed of data capture. DToF is used for Light Detection and Ranging (LiDAR) systems in consumer electronics, autonomous vehicles, and other industrial applications. - Indirect Time of Flight
Indirect Time of Flight (IToF) technology uses the phase, rather than time signature, of the reflected light to measure distance from individual points on an object. Indirect ToF technology includes a modulated light source at a set frequency. Distances are determined based on the phase difference between incoming and outgoing light. High accuracy IToF sensors perform best in short range conditions of 30 meters or less. - Structured Light
Structured light systems utilize a calibrated pattern of infrared light projected onto the object. A 3D sensing camera then detects the distortion and intensity of the pattern to determine the relative distance and shape of the object. A computer algorithm is used to reconstruct the 3D surface. Some structured light systems use phase shifted patterns or IR dots rather than a square grid. Structured light 3D scanning provides high accuracy levels with lower power consumption than time of flight sensors.
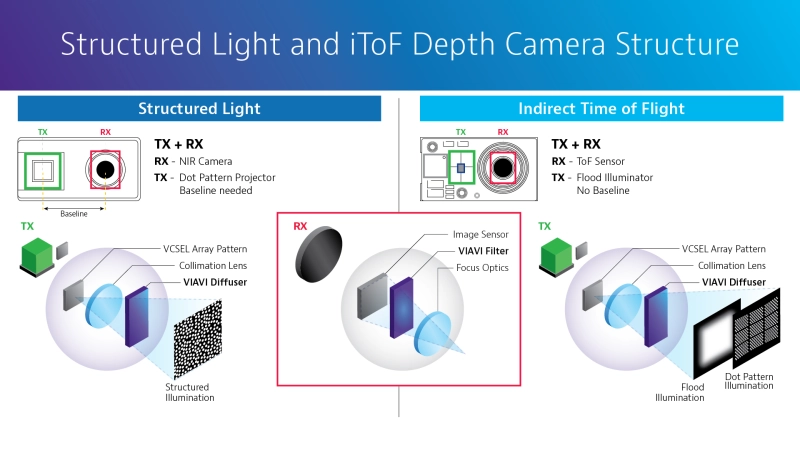
3D Sensing Components
Accurate, high resolution 3D sensing systems require all individual components to perform well together. The illumination sources for these systems are typically laser diodes or LEDs which generate infrared (IR) or near-infrared light that is invisible to the human eye. Vertical cavity surface emitting lasers (VCSELs) are a popular option due to their low energy demand, compact size, and high reliability.
- A native IR light source must be modulated though light shaping optics (LSO) that customize the irradiance and intensity for the 3D sensing application. Engineered polymers over a glass substrate are often used to diffuse the light source and eliminate “hot spots”.
- Eye safety is maintained through light shaping optics that suppress all zero-order (direct) light. VIAVI engineered diffusers control the output intensity profile while creating a uniform light field with high transmission efficiency. Diffusers are customized based on the structured light or ToF application.
- Controlling optics, including narrow-bandpass filters with high signal-to-noise ratios, prevent extraneous light from reaching the sensor. Precise filtering improves system accuracy and reduces the processing burden.
VIAVI patented low angle shift (LAS) 3D sensing filters effectively block out ambient light and reduce center wavelength shift. The thin form factor is ideally suited for current and emerging ToF and structured light applications. - Depth cameras with 3D sensors transform reflected light waves into meaningful 3D data sets. The camera’s sensor scans the light source inputs and converts them into electrical energy.
- Customized firmware is used to produce digital code from the sensor information to support a variety of cutting-edge applications. 3D sensing firmware is upgraded as the algorithms and functions evolve.
3D Sensing Technology Applications
The arrival of 3D sensing is perhaps most noticeable in today’s smartphone technology. User-facing 3D scanning improves security through facial recognition while world facing 3D sensing creates new opportunities for augmented reality and high-performance depth sensing photography. As the demand for 3D camera technology continues to grow, illumination source, LAS filter, and engineered diffuser production volumes will continue to soar.
- Consumer Electronics
Biometric scanning and other new 3D sensing applications are redefining the world of consumer electronics. Laptops and tablets are expanding on the AR/VR, motion sensing, and security innovations of mobile devices. The gesture recognition capabilities of Microsoft Kinect that revolutionized the home gaming industry have expanded to multi-player 3D position sensing, facial expression detection, and touchless heart rate monitoring. - Automotive
The automotive industry once seemed like an unlikely beneficiary of 3D sensing technology. Advanced driver-assistance systems (ADAS) and autonomous vehicles enabled by 5G and the IoT have now made 3D sensing an essential part of transportation safety. LiDAR systems provide the short and long-range 3D sensing that allows vehicles to independently assess their surroundings in real time.
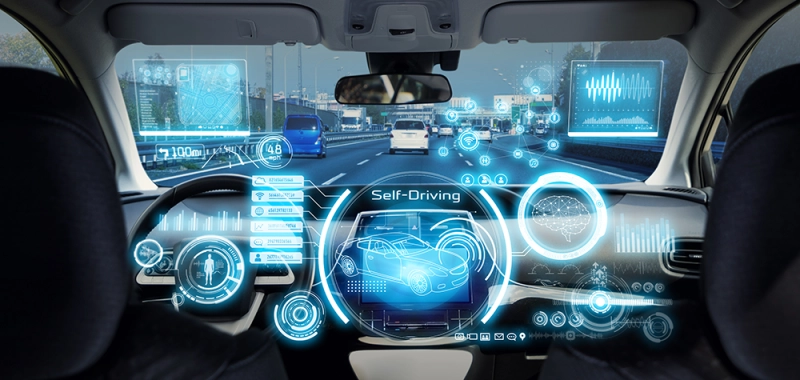
In-cabin sensing and driver monitoring systems supported by 3D cameras are used to warn drivers when they are inattentive or drowsy and facilitate gesture-driven commands. Vehicles also employ 3D scanning and facial recognition technology for ignition locks and automatic re-adjustment of driver preferences such as climate, seat, and mirror settings.
Industrial
Nimble robots operating in highly dynamic environments utilize ToF and structured light technologies to quickly identify work objects and obstacles. 3D sensing allows automated warehouse order fulfillment to be completed on a massive scale with product damage and other non-conformances detected more efficiently.
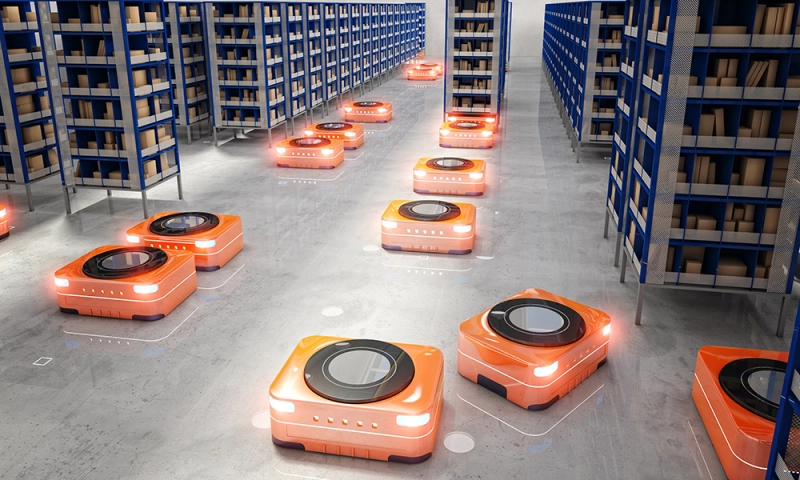
Augmented reality can be used to optimize volumetric truck and container loading patterns in much the same way a consumer might position virtual furniture in their 3D-rendered living room or try on a virtual wardrobe.
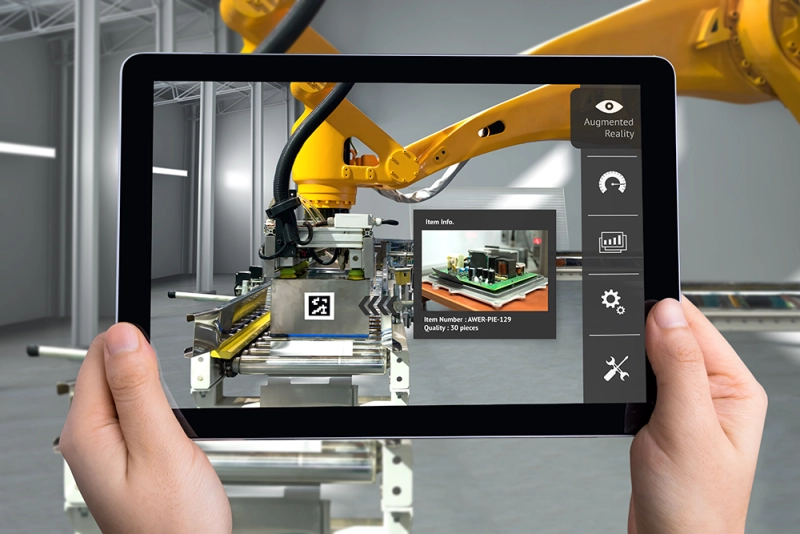
Humans, robots, and machinery operating in tight spaces can lead to safety and security issues. Potentially sensitive environments like sawmills, power plants, and data centers use 3D sensing technology to detect unsafe conditions and recognize users based on facial characteristics. Facilities and equipment are automatically shut down to avoid accidents, injuries, or unauthorized entry.
How VIAVI is Advancing the 3D Sensing Industry
Improvements to 3D sensing components and software have quickly moved ToF technology and structured light systems from niche markets into a broad range of consumer, industrial, and logistical applications.
Cell phone facial recognition was originally adopted to improve security. Today, user-created avatars and augmented reality using world facing 3D sensing have fostered unlimited creativity. At the same time, advancements in LiDAR continue to move autonomous vehicles from the drawing board to the roadway. This rapid expansion into multiple industry verticals is expected to create a $15 billion 3D sensing market globally by 2027.
With an unparalleled combination of innovation, experience, and precise, high-volume production, the patented narrow band filters and highly efficient light shaping optics pioneered by VIAVI are leading the 3D sensing industry into the next generation.
What We Offer: Precision at Scale
VIAVI is uniquely positioned to meet the demands of the 3D sensing ecosystem. Since playing a pivotal role in the development of the Microsoft Kinect gaming console, VIAVI has maintained an unwavering commitment to innovation and cost of quality.
- Patent-protected low angle shift (LAS) narrow band filters lead the industry with unmatched optical performance and high signal-to-noise ratios. These proprietary 3D sensing filters have demonstrated their consistency and reliability with over two billion units delivered to the market to date.
- Light shaping optics (LSO) with precise diffusion profiles protect eye safety by suppressing all zero-order light (no hot spots). The unique attributes of VIAVI engineered diffusers result in high transmission efficiency and uniform illumination in a scalable form factor.
- As new 3D sensing, augmented reality, and spatial awareness applications emerge, VIAVI is committed to staying ahead of the technology curve driving new LSO products and LAS filter advancements. Innovative materials and processes are continually enabling improvements to 3D sensing. As a trusted partner throughout the product lifecycle, VIAVI supports the customer journey from consulting and early prototyping to ultra-high-volume manufacturing.
Let Us Help
We’re here to help you get ahead.