光纤传感
便携式和机架安装式选件中行业领先的模块化光纤传感器
VIAVI 提供分布式温度传感 (DTS)、同步分布式温度和应变传感 (DTSS) 和分布式声波传感 (DAS) 解决方案,使用便携式 OneAdvisor 光纤传感或机架式光纤测试头-光纤传感上的布里渊 OTDR、拉曼 OTDR 和瑞利 OTDR 测量光损耗、温度、温度和应变或声波振动,以进行远程光纤测试和监控。
产品
-
FTH-DAS
利用市场上功能最全的分布式光纤振动传感解决方案来保护关键基础设施免受外部威胁,并监测管道泄露
-
FTH-DTSS
利用市场上最通用的光纤传感解决方案,监控电力电缆、管道和电信电缆的温度和应变。
-
FTH-DTS
利用市场上最通用的光纤传感解决方案监控电力电缆、管道和电信电缆的温度。
-
ONMSi 远程光纤测试系统 (RFTS)
用于核心、城域、接入和 FTTH 网络的 ONMSi 光网络管理系统。
-
OneAdvisor 800 DTS
以独特的便携式解决方案将分布式温度传感技术带到现场。利用市场上最通用的光纤传感解决方案审计、检查和维护关键基础设施。
-
OneAdvisor 1000 DTSS
以独特的便携式解决方案将分布式温度和应变传感技术带到现场。利用市场上最通用的光纤传感解决方案审计、检查和维护关键光缆基础设施。
VIAVI 提供什么类型的光纤传感测试仪?
VIAVI 光纤传感产品组合包括:
- 基于瑞利 OTDR 技术的 DTS(分布式温度传感)
- 基于布里渊 OTDR 技术的 DTSS(分布式温度和应变传感)
- 基于相干瑞利反向散射技术的 DAS(分布式声学传感)
光纤应变传感器,也称为光学应变仪,是一种使用专用 OTDR(光时域反射仪)通过称为分布式应变感测的过程来检测或感测应变的光纤。这些传感器用于测量传感器中的光变化,以检测光纤上的应变,因为沿着玻璃纤维的区域拉伸会使玻璃产生变化,直到其最终在过度应变下破裂。与传统的电应变仪不同,无源光纤应变传感器不需要持续通电,并且不受电磁干扰,电磁干扰在电应变仪系统中表现为噪声。这种噪声会导致测量结果不可读。
由于这一优势,它们的操作成本更低,并且可以在许多恶劣的物理环境中用作可靠的测量设备,对应变变化具有非凡的灵敏度。通过沿光纤传输光脉冲来测量玻璃上的应变,从而检测应变。这些类型的测量可以在现场测量过程中使用便携式 DTSS(分布式温度和应变传感器)OTDR 定期进行,也可以使用永久性、机架安装的 DTSS OTDR 在自动化例行程序中进行。光纤重量轻、价格便宜,并且可以通过在多个位置将光纤连接到待测设备来实现完全覆盖。
光纤应变传感器可用于感测不同位置的应变,例如沿管道、电信电缆、地下、沿桥梁或大型风车,以保护基础设施和人身安全,并防止环境破坏。所有声音测量过程将在安装光纤应变传感器后建立应变基准,并测量随时间的变化,如果超过规定的容差阈值,则通过自动警报触发风险通知。
光纤声学传感器是一项先进的光纤传感技术。不同于在特定点进行测量的传统传感器,分布式声学传感 (DAS) 会持续监测整个长度的光缆。光纤本身成为分布式传感元件,使其能够远距离检测和检索有关关键基础架构周围区域的振动干扰信息。
使用便携式设备(例如具有 DTS 或 DTSS 功能的 VIAVI OneAdvisor 800/1000 平台),技术人员可以前往现场对光纤进行现场测量。或者,使用 ONMSi 和具有 DTS 或 DTSS 功能的机架式光纤测试头 (FTH),NOC 可以使用定期轨迹远程监控光纤。如果相对于初始参考轨迹发生了变化,则发出警报。
使用机架安装解决方案,例如具有声学传感功能 (DAS) 的 VIAVI 光纤测试头、管道所有者/运营商和电力传输系统运营商 (TSO) 等。可以安装实时监控和报警解决方案来检测、识别、定位可能对人员、卡车、机械或手动挖掘等资产构成威胁的振动干扰,以及对此类干扰发出警报。
光纤传感作为数据点丰富的来源,安装和使用成本更低,并且所需的人工更少。线缆中的光纤构成分布式传感器,这种材料很便宜,重量轻,并且可轻松连接或嵌入到所测试的对象。
光纤是高度可靠的分布式传感器,它不需要恒定电流来生成数据,并且不会受到电磁和无线电频率干扰。在过去,沉重并且在安装时需要大量人力的有线电气式传感器一直是用于获取应变或温度数据的主要数据源。
机电传感器可能会跌落、容易被侵入且成本高昂,并且,它们还需要电源。在没有现成电源或者存在腐蚀、振动或 EMI 问题的地点,机电传感器不实用。电气和无线电噪声的进出可能会使其测量数据失真。经济高效的光纤传感器监控最适合用于需要安全监控的桥梁,在光纤传感器监控中,光纤可以嵌入或追溯性地连接到桥梁,在桥梁实际出现故障之前检测出应变和故障风险。只要光纤未过度弯曲,就能以正弦波形状安装光纤,从而在表面上形成更多的数据点。OTDR 可以检测微弯和宏弯,并且,如果应用中需要略微拉紧的光纤,则可用于在安装光纤传感器时优化光纤应变和弯曲。
光纤传感可通过光时域反射仪 (OTDR) 提供多种类型的数据,包括指示移动的声学、应变、温度和光传输特性数据,或者光纤中的弯曲和断裂。可以在整个光纤范围内获取此数据,而不局限于分散和间歇性放置的传感器位点。例如,使用 OTDR 来测量这些项目将可揭示出长跨距光纤范围内的温度梯度变化。用户还可以看到以光纤伸长表示的应变的开始和结束位置。远程通信中需要避免应变,因此对应变进行测量可以保护网络,并且可以提前缓解和修复线缆应变。如果用户想要对桥梁进行监控,光纤传感器上的应变可以指示桥梁的运动,例如下垂、下沉或桥板分离所导致的压力。
假设要对需要非常特定温度范围的建筑(例如数据中心、核电站或血库贮存设施)的温度进行测量。 传统的电气式恒温传感器放置在若干位置,并定期获取不连续点的读数。电子式温度传感器非常昂贵,而且需要持续供电。如果测量位置缺少传感器,或者传感器由于断电、极端温度或 EMI 干扰而出现故障,会发生什么情况? 温度未以最佳方式加以控制,因此产生了热点或冷点。由一条或多条光缆构成的光纤传感器网可以遍布整个建筑,从而可以在连续的位置获取读数。光纤网可提供更多数据点,以更低的成本实现更大的覆盖范围,并且可靠性更高。只需要激光器 OTDR 发出的光脉冲便可询问光纤传感器,并且在断电的情况下可以通过电池对设备进行超过一天的供电。
此外,分布式声学传感 (DAS) 提供关于传感光纤沿线的声音频率和振动信息,提供有关资产周围环境中发生的振动干扰的持续和动态实时信息。这增强了威胁检测功能,能够迅速检测和定位从安全边界漏洞到计划外的建设工作(例如人工或机械挖掘)再到环境危害或事件在内的特定外部威胁。它能提供迅速做出反应和保护资产所需的关键情报,以便识别和定位威胁。
光纤传感器有哪些变革性的应用?
全球各地的通信电缆都布置在崎岖荒凉的地下、海底和高空环境中,在这样的环境中,冰、风、地球运动/侵蚀、波浪、破坏行为以及人为错误都会不断使线缆产生应变或者断裂,从而导致服务中断和服务降级。在安装过程中,有时也会意外地使线缆产生应变。一旦发生过度应变,线缆就面临断裂的风险,并且线缆的寿命也会从 35-40 年大幅减少到仅仅数月。
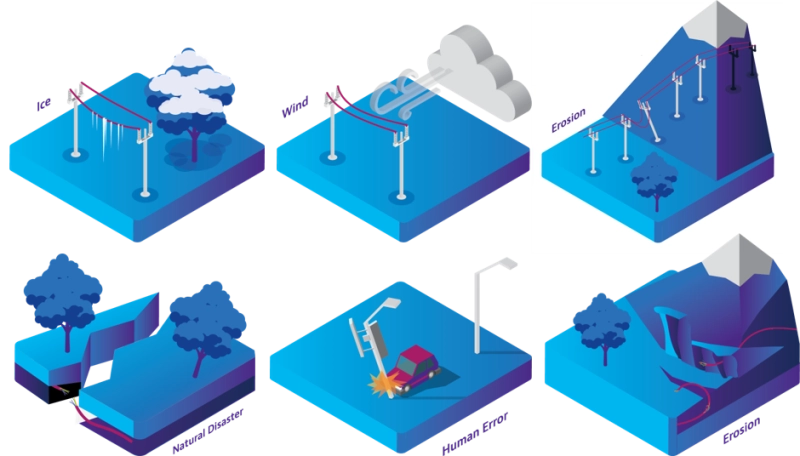
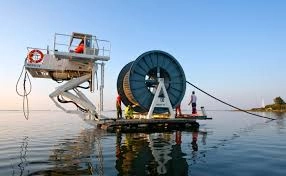
长距离线缆和海底线缆非常重要,而在出现恶劣天气或处于偏僻、危险的地势中时,维修非常困难。通过使用光纤传感器完成的分布式应变传感,网络线缆所有者将能在安装时对光纤进行测试,然后监测暗纤是否有过度应变风险,并在维修过程中监测应变的变化,从而减少破损。毛里塔尼亚最近遭受了一次海底线缆断裂事故,造成整个网络与互联网断开长达两天。导致这次事故的原因是一艘拖网渔船将非洲海岸到欧洲的线缆从海底拔起并拉断。假如对此线缆进行了应变监控,在线缆被拔起拉断之前就会触发警报。如果线缆最终断裂,经典的瑞利 OTDR 可在一米的误差范围内找到断裂处,从而缩短运行中断时间。长距离线缆和海底线缆非常重要,而在出现恶劣天气或处于偏僻、危险的地势中时,维修非常困难。通过使用光纤作为传感器进行传感的分布式应变传感,网络线缆所有者将能在安装时对光纤进行测试,然后监测暗纤是否有过度应变风险,并在维修过程中监测应变的变化,从而减少破损。使用分布式声学传感进行监测,可检测临近的威胁,比如渔网或船锚。毛里塔尼亚最近遭受了一次海底线缆断裂事故,造成整个网络与互联网断开长达两天。导致这次事故的原因是一艘拖网渔船将非洲海岸到欧洲的线缆从海底拔起并拉断。假如对此线缆进行了应变或声学监控,在线缆被接近和拔起拉断之前就会触发警报。如果线缆最终断裂,经典的瑞利 OTDR 可在一米的误差范围内找到断裂处,从而缩短运行中断时间。
假设一条高空线缆负冰过重。网络运营商可以对线缆进行监控,并安排工作人员对有需要的网段进行除冰,从而防止产生过度应变。发生应变事件后,可以依据 MAT 容差测量结果对线缆进行测试,从而确定更换优先级。可提供便携式 DTSS 光纤传感器 OTDR 和机架安装式光纤询问 OTDR。
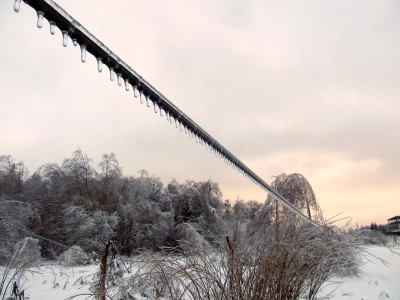
线缆断裂的最常见原因是施工挖掘(也称为挖掘机衰减)。 通常在找到断裂后,会在断裂位置对线缆进行接合或连接。但是,这只能暂时解决问题,因为当挖掘机将线缆从地下拉出时,应变已经损坏了断裂位置两侧的数米线缆。
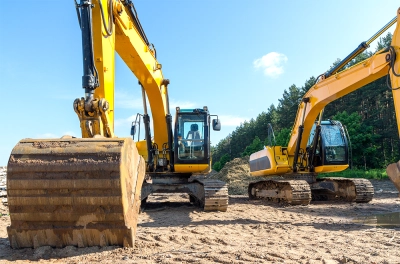
线缆在重新安装时可能会再次断裂,或者过度损坏导致性能严重降低,以至于无法提供充分的服务。重复进行维修成本高昂,并且导致服务多次中断。通过在出现断裂时在线缆的上下两个方向上使用光纤传感器 OTDR 进行分布式应变测量,技术人员可以提供科学证据来精确地展示应更换线缆的哪些部分。可以使用此证据来向责任方追讨损坏费用。它可防止后续重复派遣维修人员并造成客户服务中断,也可避免不必要地维修没有遭受应变损坏的正常线缆部分。
在石油行业、化工行业、食品行业、废品行业和水利行业中,使用管道运送各种类型昂贵并且可能有腐蚀性的物质。溢漏、造成污染物进入管道的泄漏或者盗窃可能会导致灾难性的问题。通过测量管道沿线光纤的温度和应变,可以实现管道监控。 同样,也可以用类似的方式对堤坝进行监控。如果光纤的温度或者应变或光反射特性发生大幅变化,则疑似存在泄漏。温度变化可能指示泄漏或偷盗,应变可能指示由于意外运动而存在断裂的风险。并且,通过使用传统的光反射瑞利散射 OTDR 分析可以在一米的误差范围内确定问题的位置。在机架安装式 OTDR 监控解决方案中,可以使用针对应变、温度和光反射的光测试仪组合来持续监控连接到管道的光纤传感器。光纤传感器提供准确的检测,从而可快速完成关闭、检测和维修过程。
电力传输设备上的电热点会造成危及生命的火灾风险和基础设施损坏。 美国加利福尼亚州最近就发生了这样一个例子,当时,一处电热点或掉落的电力电缆可能引发了一场森林火灾。这场火灾造成了生命和财产损失,涉事电力公司正面临着诉讼和破产风险。
使用分布式温度传感 (DTS) 实现的远程光纤传感是监控此类问题唯一经济的方式,与这种灾难性事件的代价相比,成本要低廉得多。光纤放置在输电线路沿线,用于对线路进行远程监控。 当光纤传感器系统检测到温度上升、应变或可能表示线路掉落的弯曲时,便会触发警报。通过将该系统与瑞利 OTDR 分析结合使用,可以将参考轨线与恒定的定期轨线进行比较,从而在光纤位置发生渐变或突变时确定精确位置。警报可以触发紧急断电和对输电线路的调查。由于使用光纤传感器的光纤分析不受 EMI 的影响,因此在这种高 EMI 环境中,它是理想的数据来源。
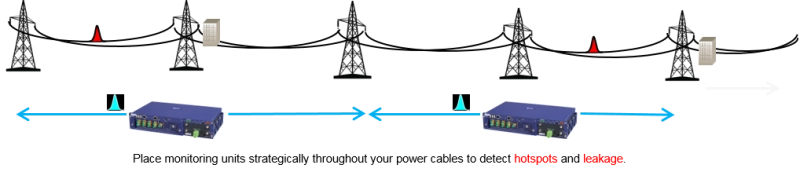
每一阶段的支持
我们提供您所需的支持、服务、全面培训以及资源。这只是我们为最大程度提升您投资的价值所作努力的一部分。
咨询专家
请与我们联系以了解详细信息或获取报价。不管您有任何疑问,都可以咨询我们的专家来获得正确解答。